As discussed earlier the equipment of a sheet metal shop varies widely depending upon the size of the product and production quantities. The layouts also vary accordingly. A reasonably equipped sheet metal fabrication shop should have at least the following:
Primary Section
- Sheet stalkers
- Power Shearing Machine, 2.5 Mt length, Hand Shears
- CNC Turret Punch Press, 24 stations, Power Presses- 20T,60 T, Fly Presses
Secondary Section
- CNC Press brake 2.5 Mt length, Hydraulic press brake. 2.5 Mt, Folding machine 1.2 Mt
- Notching Machine, Clinching machine, Riveting machine, Hand Riveting equipment
- Work Benches 2Mt length, Fitter Hand Tool Sets,
Integration Section
- CO2 Welding, TIG Welding, Arc Welding, Spot welding, Resistance welding
- Welding Tables, Welding Jigs
- Deburring, Grinding, Sanding
- Inspection Tables, Inspection Tools
Finishing Section
- 7 Tank Pre-treatment
- Conveyorized Spray painting, Powder Coating booths
- Effluent Treatment Systems
- Plating Systems
Assembly Section
- Assembly tables
- Assembly Documents
- Assembly jigs
- Pneumatic Screwdrivers
- Cleaning Systems
Dispatch Section
- Packing
- Dispatch Documents
- Jib Crane or other lifting equipment
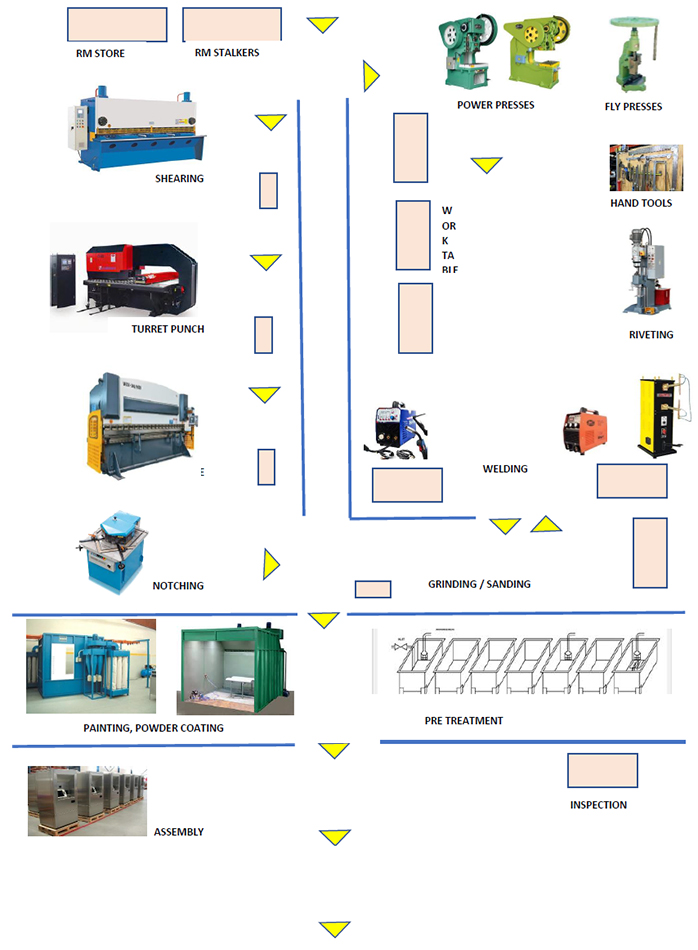
TYPICAL LAYOUT OF A SHEET METAL FABRICATION SHOP. MACHINES CAN BE MORE THAN ONE.
Production should be planned based on firm BOM and BOQ along with formatted final drawings, not as-built drawings
Sheet Metal production initiation generally comprises of:
- Work Order Generation
- Production Flow path creation
- Man, and machine time planning
- Quality manual generation
- Inspection manual generation
- Dispatch document generation
The production begins with these documents. There must be periodic in-process quality checks and final quality checks before the product is certified for dispatch.